Layout analysis to improve the productivity of the welding process in an agricultural equipment factory
DOI:
https://doi.org/10.47456/bjpe.v9i5.42675Keywords:
Productivity, welding, layout, flowchart, spaghetti diagramAbstract
Evaluating and improving productivity in the welding process in the manufacturing industry is a great challenge for factory engineering personnel and managers. In this sense, the purpose of this study is to reduce the movement of welders during the manufacture and welding of a chassis of agricultural machines through layout analysis and process flow chart. The object of this study was defined as the workstation with the lowest productivity index, from this definition, proposals were created for new layout and process flow chart applying the spaghetti diagram tool that made it possible to understand current scenario related to movements, intersections of paths, distances traveled and physical arrangement of all components that make up a workstation, required during the work cycle. These analyzes and applications have resulted in a new definition of the labor qualification level for welders in the workstation, as well as a 12% reduction in the area occupied and 22% reduction in the distance traveled. Simply put, it proved to be a useful tool for these analyzes.
Downloads
References
Barnes, R. M. (1977). Estudo de movimentos e de tempos: projeto e medida do trabalho. 6 ed. São Paulo: Edgard Blucher.
Brant, D. (2020). Spaghetti charts and physical distancing. The Lean Global Networking Journal. Recuperado de: https://planet-lean.com/spaghetti-chart-physical-distancing/
Choudhury, B. & Chandrasekaran, M. (2017) Investigation on welding characteristics of aerospace materials – A review. Materials Today: Proceedings. 4(8), 7519-7526. https://doi.org/10.1016/j.matpr.2017.07.083 DOI: https://doi.org/10.1016/j.matpr.2017.07.083
Cortés, D.; Ramírez, J.; Ponce, P. & Molina A. (2021). S3Manufacturing process taxonomy. Journal of Manufacturing Processes. 67, 579-610. https://doi.org/10.1016/j.jmapro.2021.04.069 DOI: https://doi.org/10.1016/j.jmapro.2021.04.069
Daneshjo, N.; Rudy, V.; Malega, P. & Krnáčová, P. (2021). Application of Spaghetti Diagram in Layout Evaluation Process: A Case Study. TEM Journal. 10(2), 573‐582. https://doi.org/10.18421/TEM102-12 DOI: https://doi.org/10.18421/TEM102-12
Groover M. P. (2010). Fundamentals of Modern Manufacturing: Materials, Processes, and Systems. 4. ed., United States of America: John Wiley & Sons, Inc.
Niemann, J.; Reich, B. & Stöhr, C. (2021) Lean Six Sigma: Methoden zur Produktionsoptimierung. Springer Vieweg. 2021. https://doi.org/10.1007/978-3-662-63008-2 DOI: https://doi.org/10.1007/978-3-662-63008-2
Omar, M.A.; Elerian, F.A.; Soltan, H.A. & Ghattas, M.S. (2018). An Integrated Approach for Welding Process Selection. Mansoura Engineering Journal. 43(1), 1-6. https://doi.org/10.21608/bfemu.2020.94524 DOI: https://doi.org/10.21608/bfemu.2020.94524
Okpala; Chikwendu, C.; Chukwumuanya & Okechukwu. (2016). Plant Layouts’ Analysis and Design. International Journal of Advanced Engineering Technology. 7(3), 201-206.
Peinado, J. & Graeml, A. (2007). Administração da Produção (Operações Industriais e de Serviços). Curitiba: UnicenP.
Senderská, K.; Mreas, A. & Vaclav, S. (2017). Spaghetti Diagram Application for Workers’ Movement Analysis. U.P.B. Sci. Bull. 79(1), 139-150.
Singh, M. (2012). Innovative practices in facility layout planning. International Journal of Marketing, Financial Services & Management Research, 1(12), 126-139.
Slack, N.; Jones, B A. & Johnston, R. (2018). Administração da Produção. 8. ed. São Paulo: Atlas
Sreekumar, M. D.; Chhabra, M. & Yadav, R. Productivity in Manufacturing Industries. International Journal of Innovative Science and Research Technology, 3, (10)
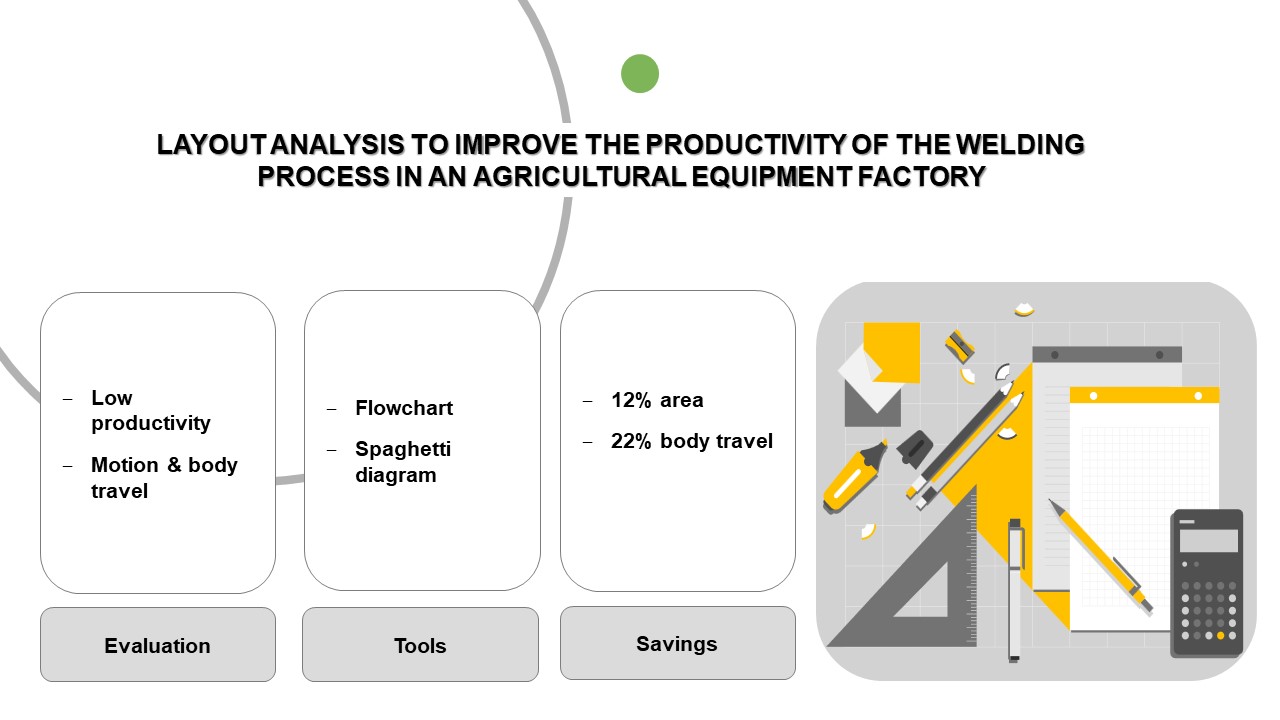
Downloads
Published
How to Cite
Issue
Section
License
Copyright (c) 2023 Brazilian Journal of Production Engineering

This work is licensed under a Creative Commons Attribution-NonCommercial-ShareAlike 4.0 International License.
